Cracks, Cost, and Confidence: Why Fracture Toughness Matters More Than Ever
Fracture toughness helps assess flaw risk in infrastructure; ABI® testing offers fast, non-destructive, in-service evaluation for safer, cost-effective decisions
By: Clark Ellis, Senior Vice President & Fahmy Haggag, Chief Engineer, ABI® Technology
WHAT IS FRACTURE TOUGHNESS? Initiation fracture toughness is a physical property of materials which characterizes the amount of deformation energy required to advance the length of an existing crack in a specimen or a structural component. Sharp cracks in a steel structure might advance, due to service conditions, either slowly in a ductile fashion or quickly/catastrophically in a brittle/cleavage fashion depending on the flow properties, temperature, and applied stresses. Fracture toughness, therefore, is essentially the ability of the material to resist cracking whether slowly or quickly.
Why is it important to know for infrastructure?
All materials, no matter how they are processed, inherently contain a certain amount of flaws. These could be a metallurgical inclusion, void, a crack, or any combination. Since flaws cannot be avoided, engineers often use a specific flaw size and number of flaws to design critical components. To ensure that materials meet the requirements for their applications, two frameworks are used: Fitness for Service (FFS) and Risk Based Inspection (RBI). Data critical to FFS and RBI include fracture toughness, yield strength and other mechanical properties of a specific material. This provides the data that owners need to make informed decisions about whether to continue operating a piece of equipment, such as a pipeline or process equipment, or structure, by increasing the inspection cadence, or shutdown to repair or replace a component.
For example, in evaluating the FFS of a pipeline that has a small pit or a small crack, the specified grade of the pipe is only a starting point. It defines the minimum ability of the designed pipe (no flaws of pits or cracks) pipe to withstand the operating conditions. Knowing the actual fracture toughness properties enables the operator to know with confidence (based on accurate Level 3 FFS) that they can continue operating a pipeline that, has a minor anomaly, without having to shut it down for an immediate repair or replacement. If this allows the operator to schedule a repair for a planned shutdown that occurs in 3 months, that can save hundreds of thousands of dollars if not millions of dollars in lost production or transmission service.
RBI programs are similarly impacted by having accurate fracture toughness data for specific equipment, pipelines or vessels. Knowing the true strength of a component allows the operator to design and adjust its RBI resource allocation model for the most appropriate inspection cadence. This allows the most effective use of its inspection methods and resources, ensuring that they are deployed where they are most needed. For example, taking the pipeline anomaly described in the prior paragraph, Fracture Toughness data allows the operator to determine the appropriate cadence or frequency of inspection to monitor to ensure that the anomaly hasn’t grown or advanced to the point where it requires further action. By deploying inspection resources where they are most needed and not deploying them where they are not needed, the operator’s system asset integrity is best protected, while maximizing their resources.
Fracture Toughness analysis is a unique and vital tool for asset integrity teams as it provides specific and accurate guidance on how to safely reduce risks and the costs of remediation, while optimizing deployment of asset inspection teams by improving the accuracy of RBI models. At the end of the day, asset integrity is about operators making good, informed decisions about monitoring, inspecting, repairing, and replacing components at the appropriate time. Fracture Toughness values help ensure operators that they are targeting their asset integrity efforts so that they optimize safety and productivity and reduce their risk.
How is it traditionally measured?
Carbon and low alloy steels (used in oil and gas pipelines, storage tanks, pressure vessels, bridges and structures, etc.) fracture according to one of two mechanisms (critical fracture stress for brittle fashion/mode or critical fracture strain for the ductile fashion). Hence, it is very important to determine the initiation fracture toughness of the material to avoid service failure. For laboratory destructive fracture toughness testing, a specimen is machined with a notch and the notch is sharpened with fatigue pre-cracking and then the specimen is pulled apart using a testing machine.
For ductile behavior, the fracture toughness value is determined from the deformation/pulling energy (J-integral) until the crack advanced slightly (by the empirical/small value of 0.008 inches or 0.2 mm) because experimentally it is very difficult to determine the true deviation from the crack blunting line or the first point of initial slow crack extension.
For brittle/cleavage behavior, the fracture toughness is determined from the deformation energy (J-integral) until the specimen fractures by cleavage.
Non-Destructive Alternatives to Destructive Laboratory Testing
Destructive testing in a laboratory continues to be one of the important tools for asset integrity groups to assess the fracture toughness values associated with their equipment or infrastructure. These tests are time consuming and are costly both in terms of the test itself, but more importantly in terms of the downtime often required to execute the test. This results in organizations being very selective in how they deploy this critically important test. If owners could perform more fracture toughness tests across their assets this data would aide their decisions about maintenance, repairs, and replacements, leading to safer, more reliable, and more productive assets.
Automated Ball Indentation® (ABI®) is a non-destructive testing methodology that determines Fracture Toughness and Tensile properties of ferritic steels. It provides an alternative to destructive lab testing as it can be deployed on-site while assets are in operation. It’s faster, less costly and provides fracture toughness test results with a minimum or no disruption to ongoing operations.
In an ABI® test, the initiation fracture toughness is determined from the indentation deformation energy until a critical indentation depth is reached according to the attained test material fracture mechanism. This means that this non-destructive method uses a test measurement (ABI® deformation energy) and one fracture mechanism depending on the flow properties and the test temperature.
The critical fracture strain model/criterion, for Ductile fracture is empirical while the critical fracture stress model, for Brittle fracture is semi-empirical.
The ABI® fracture toughness values have been compared against those values from destructive tests of various ferritic steels, such as pipeline steels and from storage tanks with excellent agreement. The new ABI® method has two major advantages:
- It is non-destructive where no cutting of material is required and may be performed while the equipment remains in service.
- The test is valid for all thicknesses of ferritic steels, such as pipelines, vessels, tanks, and other structures with strengths from 30-140 ksi [207-965 MPa].
The reasons for the ABI® test method’s success are:
- The tri-axial nature of the ball indentation which creates a high value of stress concentration (exceeding that ahead of a crack-tip) although no cracks could be formed because of the high constrain of the deformed plastic material surrounding the indentation.
- The true value of initiation fracture toughness value is the deformation energy when a crack starts increasing near zero value; allowing the use of a ball indentation deformation energy up to a critical indentation depth (depending on the attained fracture mechanism).
Since it is non-destructive and can be conducted in the field on assets that are in operation, the ABI® test method can save significant time and cost as compared with existing destructive fracture toughness test methods. Asset owners who add ABI® to their asset integrity testing portfolio can deploy physical material testing across their infrastructure with lower cost per test and faster results. This will allow them to make better decisions on maintenance, repair, and required replacement and to continue safe operations even as infrastructure ages.
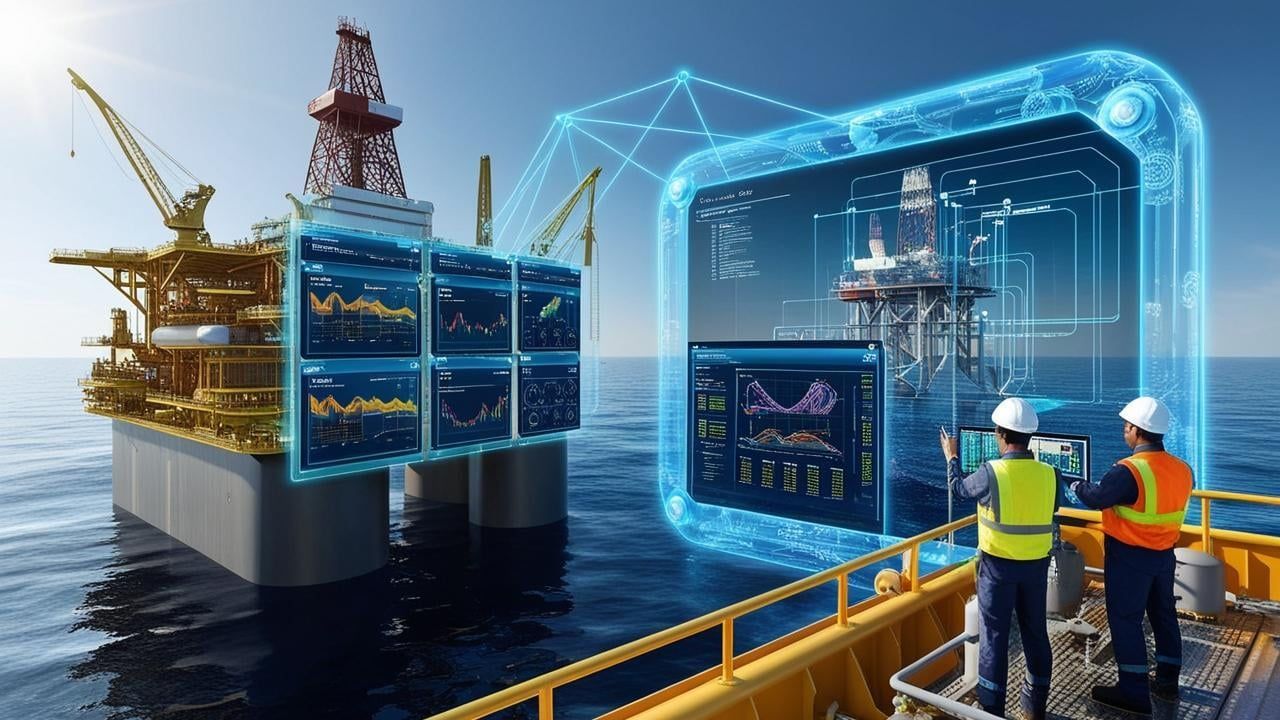