Fracture Toughness Takes on Higher Importance in Cold Temperatures and Other Embrittlement Conditions
Fracture Toughness Takes on Higher Importance in Cold Temperatures and Other Embrittlement Conditions
Most organizations tend to focus on material grade and tensile properties when evaluating their assets. Traditional means of measuring fracture toughness requires destructive testing which is costly, time consuming, and often requires assets to be shut down while the tests are conducted. Because of these constraints, fracture toughness testing is done infrequently.
However, when assets are operated in cold environments offshore, in extreme northern geographies, or that involve carrying or processing products that are either transported at low temperatures or can cause embrittlement, knowing the fracture toughness of the asset material is crucial to safe operations. Pipeline steels (e.g. API 5L Grades) become more susceptible to hydrogen-assisted cracking (HAC) at an accelerated rate in colder environments.
Operators can use lower cost Non-Destructive Testing (NDT) methods like Automated Ball Indentation® (ABI®) to increase the testing frequency for assets that are operated under cold temperatures or that carry products that accelerate embrittlement or are very cold, themselves. This produces more data that can provide direct insights into the fracture toughness and Fitness for Service (FFS) for those assets. The data can also feed asset integrity analytics systems that can help predict asset behavior and can prevent incidents and improve overall system safety and productivity.
Case Study: Hydrogen Embrittlement Analysis Using Automated Ball Indentation® (ABI®)
Monitoring hydrogen embrittlement is required for the safe transmission of hydrogen in ferritic steel pipelines. Given that the chemical composition and microstructure of pipeline steels are key factors affecting their susceptibility to hydrogen embrittlement, several grades of pipe were investigated in this project, and their tensile and fracture toughness properties were non-destructively measured as a function of exposure time to hydrogen pressure. Grade X80 steel was received from a commercial vendor who performed destructive fracture toughness testing on the material (outer diameter of 406 mm and wall thickness of 14.6 mm). The conventional testing used 0.5T CT specimens that were soaked in hydrogen for 30 minutes before their testing according to ASTM Standard E1820 for initiation fracture toughness (JIc). Destructive testing showed that the fracture toughness decreased from 225 MPa√m (zero hydrogen pressure) to 118 MPa√m (13.79 MPa or 2000 psi hydrogen pressure), i.e. a 48% reduction due to hydrogen embrittlement. The microstructure of the X80 pipeline steel consisted of bainite or tempered martensite with fine grains and low inclusions.
Conventional fracture toughness testing has two disadvantages, namely, using large amounts of hydrogen for purging the autoclave prior to testing and pressurizing the autoclave during testing, and for exposing the specimen from both sides (although in a pipeline transmission the pipe wall is hydrogen pressurized only on the inside surface). The ABI® method and the hydrogen chamber of this investigation have several advantages over conventional destructive testing: nondestructive, in-situ, use of a very small volume of hydrogen per experiment, use multiple pipeline steel specimens exposed to the same hydrogen pressure and purity per single experiment, and conduct multiple ABI® tests on each disc sample.
The hydrogen chamber was designed to contain six disc samples, each of 25-mm diameter and 9.5-mm thick. It used a total volume of 36000 mm3 (1.3 in3). The testing head of the system was temporarily attached to the top ferritic steel plate of the hydrogen chamber with a magnetic mount to perform ABI® tests at various locations on each disc sample at various exposure times to monitor hydrogen embrittlement. The outer surface of each sample was sufficient to perform 16 ABI® tests per disc sample. Due to the small volume of hydrogen, it was safely released in air after the end of the experiment (200 hours). Several pipeline materials of Grade B, X52, X70, and X80 were included in the experiment, and in-situ ABI® tests were conducted after 13.79 MPa (2000 psi) hydrogen exposure of 5, 25, 100, and 200 hours. Changes in the tensile and fracture toughness properties due to hydrogen pressure exposure for various times were measured from the in-situ ABI® tests.
The ABI-determined fracture toughness of X80 pipeline steel decreased by 12%, 25%, 32%, and 30% after 13.79 MPa (2,000 psi) hydrogen exposure times of 5, 25, 100, and 200 hours. The reduction in fracture toughness appears to saturate at 100 hours for the 9.5-mm 0.375-inch) thick sample.
This compared well with the 48% reduction in fracture toughness of 0.5T CT samples tested in an autoclave. The complete immersion in hydrogen is more severe than actual hydrogen pipeline transmission application. The hydrogen pressure chamber better simulates a pipeline steel application since the samples are exposed to hydrogen pressure only on their inside surface. ABI® testing can be performed on the outer surface of in-service hydrogen transmission pipelines at various times to monitor their actual hydrogen embrittlement.
No reduction in fracture toughness was observed for disc samples manufactured from Grades B, X52, and X70 included in the same experiment with the X80 steel. The increase in tensile properties was very small for the X80 pipeline steel and no changes were observed for other grades.
Operators can use ABI® to improve their monitoring of assets that operate in cold conditions or that carry products that accelerate embrittlement. It can be leveraged as a pre-screening tool to determine yield strength and fracture toughness in field locations as well as a critical data point for digital twin models and degradation trend tracking.
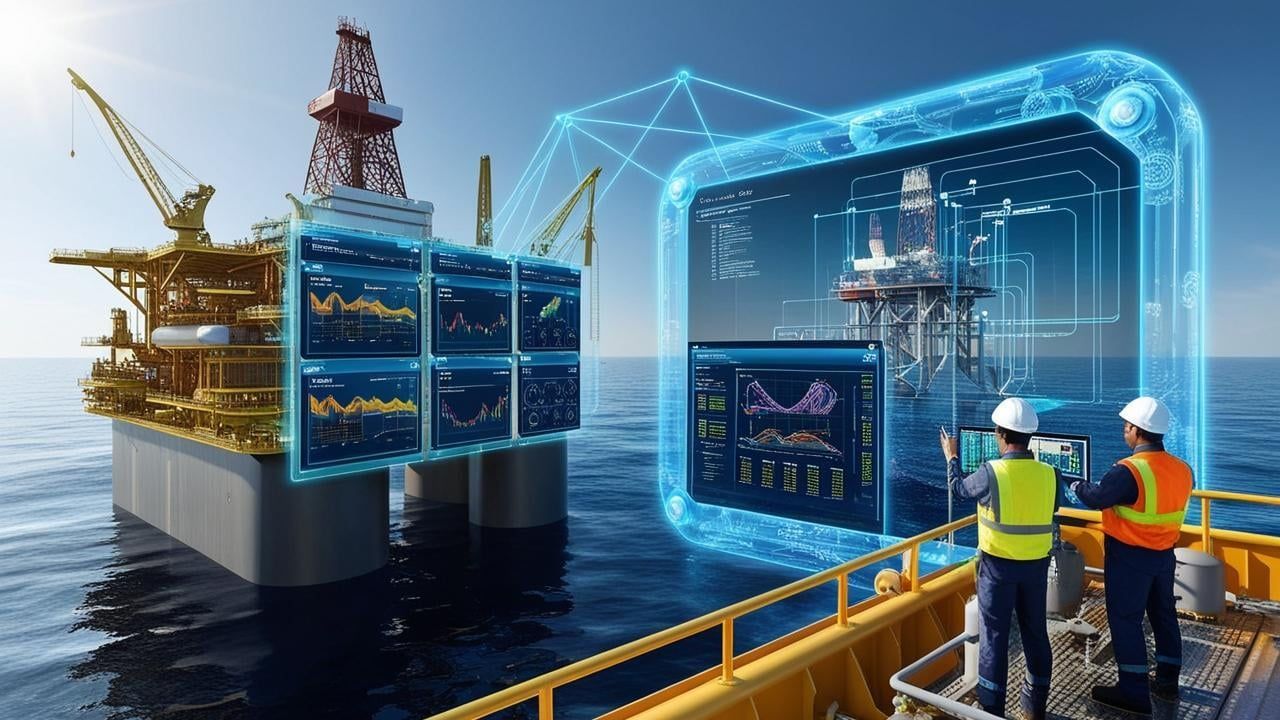